A few years ago, we implemented a system that assist us to organize and clean up work areas. By integrating these standards, we have sped up production, minimized mistakes, and are creating an organized area.
Currently, we have been focusing on our receiving area. With the issues with getting certain materials from suppliers, we have been ordering other components well in advanced. That ensures that once backordered supplies arrive at our facility, we are ready to build. As you can imagine, having more materials in the facility has given us a space issue.
We have increased our raw materials over 70%. This increase lets us provide better delivery dates and reduce gaps in production time.
Our receiving department also houses our picked parts. We have been organizing spaces to accommodate new materials, and also going through our stock. Any items that are not picked on a regular basis will be put in a designated inventory area. This opens up space to ensure regularly required parts are accessible. While all of this organizing is happening, it gives us the ability to do a more in depth inventory count.
An area that was once our winding department now houses engines and gen ends.
We are adding more sort bins to utilize shelf space and ease of access.
As WINCO continues to grow, our need for space will be an ongoing, but welcomed challenge. Stay tuned to find out more about how our facility prepares for the future!
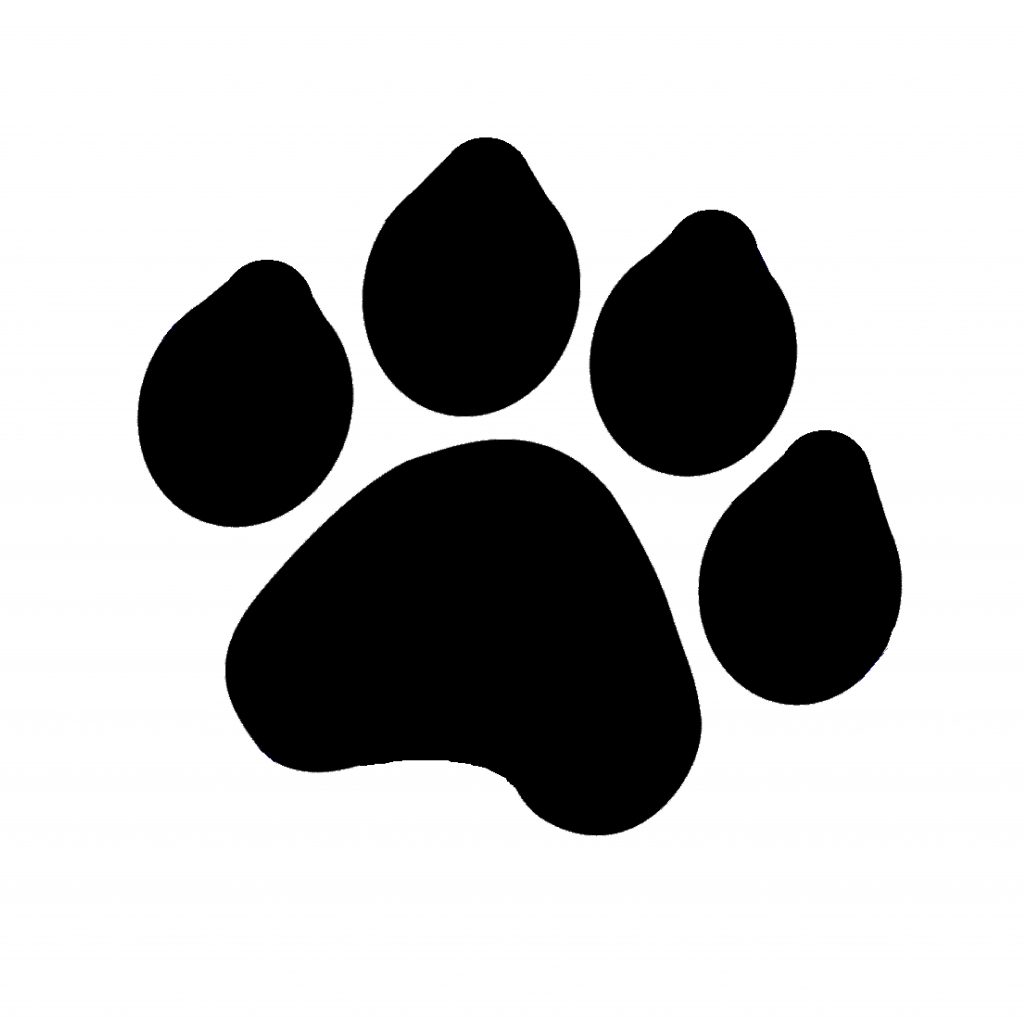